Checking Out the Different Strategies and Technologies Behind Plastic Extrusion
The realm of plastic extrusion is a mix of modern technology, precision, and technology, essential to numerous markets worldwide. Advanced equipment, electronic controls, and an array of materials converge in this intricate procedure, producing top quality, resilient products.
Understanding the Fundamentals of Plastic Extrusion
The process of plastic extrusion, typically hailed as a keystone in the world of production, develops the bedrock of this discussion. In essence, plastic extrusion is a high-volume manufacturing process in which raw plastic material is melted and formed into a continual account. The procedure starts with feeding plastic products, commonly in the type of pellets, right into a heated barrel.
The Role of Different Products in Plastic Extrusion
While plastic extrusion is a commonly utilized technique in manufacturing, the products utilized in this procedure greatly influence its last result. Different types of plastics, such as abdominal, polyethylene, and pvc, each lend one-of-a-kind residential or commercial properties to the end item. Polyethylene, known for its longevity and versatility, is often made use of in packaging, while PVC, renowned for its strength and resistance to ecological factors, is made use of in building. ABS, on the various other hand, combines the most effective characteristics of both, causing high-impact resistance and durability. The selection of material not just impacts the product's physical residential or commercial properties however also impacts the extrusion rate and temperature. As a result, manufacturers need to meticulously think about the buildings of the material to enhance the extrusion procedure.
Methods Utilized in the Plastic Extrusion Process
The plastic extrusion process involves numerous strategies that are critical to its procedure and effectiveness (plastic extrusion). The conversation will start with a streamlined explanation of the basics of plastic extrusion. This will be adhered to by a failure of the procedure thoroughly and an exploration of approaches to improve the efficiency of the extrusion technique

Comprehending Plastic Extrusion Basics
In the realm of production, plastic extrusion stands as a fundamental process, necessary in the manufacturing of a wide range of daily things. At its core, plastic extrusion entails transforming raw plastic material into a constant profiled form. This is attained by thawing the plastic, often in the form of pellets or granules, and requiring it via a designed die. The resulting item is a lengthy plastic item, such as a pipe, wire, or panel covering, that maintains the form of the die. This economical approach is very functional, able to develop complicated shapes and fit a variety of plastic products. Essential understanding of these fundamentals enables for additional exploration of the more complex aspects of plastic extrusion.
Detailed Extrusion Refine Malfunction

Improving Extrusion Technique Effectiveness
Efficiency gains in the plastic extrusion procedure can significantly impact both the quality of the last item and the general efficiency of the operation. Continual optimization of the extrusion strategy is essential to keeping an affordable edge. Normal upkeep of extrusion tools can likewise decrease downtimes, hence boosting efficiency.
Just How Technology Is Changing the Face of Plastic Extrusion
The arrival of new technology has actually dramatically transformed the landscape of plastic extrusion. It has brought about the advancement of advanced extrusion equipment, which has boosted the effectiveness and quality of the plastic extrusion procedure. Moreover, developments in the extrusion procedure have additionally been driven by technological advancements, using improved capacities and adaptability.
Advanced Extrusion Equipment
Transforming the realm of plastic extrusion, progressed equipment imbued with cutting-edge innovation is ushering in a new era of performance and accuracy. These makers, geared up with innovative attributes like automatic temperature control systems, ensure optimum problems for plastic processing, thereby decreasing waste and improving product top quality. While these improvements are already impressive, the constant evolution of modern technology guarantees even better leaps onward in the field of plastic go to this website extrusion equipment.
Advancements in Extrusion Processes
Using the power of contemporary innovation, plastic extrusion processes are undertaking a transformative metamorphosis. Innovations such as electronic mathematical control (CNC) systems now Full Article enable even more accuracy and consistency in the manufacturing of extruded plastic. Automation even more boosts efficiency, lowering human error and labor expenses. The integration of expert system (AI) and device learning (ML) formulas is revolutionizing high quality control, forecasting discrepancies, and improving the total performance of extrusion processes. With the arrival of 3D printing, the plastic extrusion landscape is also broadening right into brand-new realms of possibility. These technical innovations are not only improving the high quality of extruded plastic items yet additionally pushing the market in the direction of a more sustainable, effective, and ingenious future.
Real-World Applications of Plastic Extrusion
Plastic extrusion, a flexible and effective process, finds use in plenty of real-world applications. It's predominantly used in the production market, where it's used to produce a myriad of products such as pipelines, tubes, window frames, weather removing, and fence. The automobile industry additionally utilizes this innovation to produce components like plastic and trim sheet. Additionally, the clinical area counts on extrusion for the fabrication of catheters, IV tubes, and other clinical gadgets. Even in food production, extrusion plays a duty in developing items like pasta or grain. The strength and flexibility of plastic extrusion, combined with its cost-effectiveness, make it an important process throughout different industries, highlighting its widespread functional discover this applications.
The Future of Plastic Extrusion: Patterns and forecasts
As we look to the horizon, it comes to be clear that plastic extrusion is positioned for considerable developments and transformation. Green options to conventional plastic, such as bioplastics, are also anticipated to obtain traction. These trends suggest a dynamic, advancing future for plastic extrusion, driven by technological innovation and a dedication to sustainability.
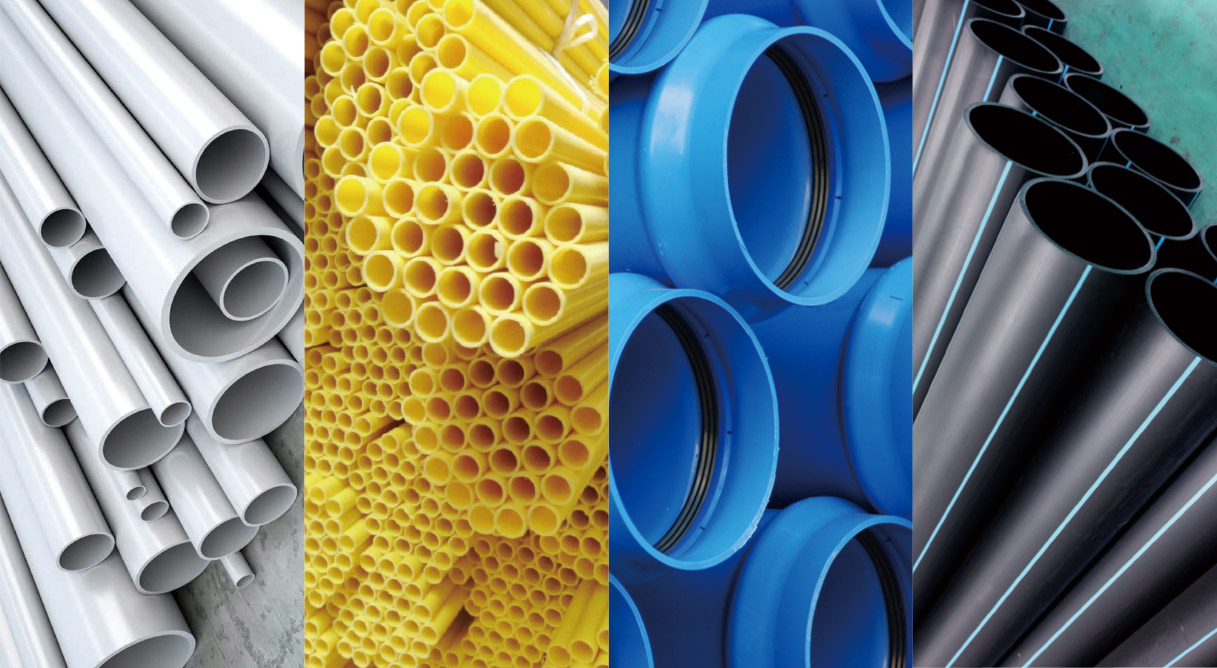
Verdict
In conclusion, plastic extrusion is a complex procedure that makes use of sophisticated innovation and varied products to produce diverse items. As plastic production continues to advance, it remains a vital part of several sectors worldwide.
In significance, plastic extrusion is a high-volume production procedure in which raw plastic product is melted and created right into a constant profile.While plastic extrusion is a commonly made use of method in production, the products used in this procedure substantially influence its last outcome. At its core, plastic extrusion involves changing raw plastic material right into a continuous profiled form. It has led to the growth of sophisticated extrusion equipment, which has boosted the effectiveness and top quality of the plastic extrusion process.In verdict, plastic extrusion is a complicated procedure that uses innovative innovation and differed materials to produce varied products.